TMA Bark’s Operations Director, Shane Andrews, describes how his specialist producer of growing mediums manages wood and garden waste using a wide range of Komptech equipment.
Processing organic waste can cover a wide spectrum of activity, which is especially true for TMA Bark, as it has grown from its early beginnings as a specialist bulk haulier to becoming one of the largest producers and market leaders in the UK for bark, mulch, and woodchip products, as well as compost.
According to Shane Andrews, its Operations Director, the company’s development in this space can be traced back to a chance encounter: “The business started off as a transport business, run by my family. One day my dad was approached by someone wanting to get rid of some bark. He’s quite mechanically minded, so with my grandad, they built a very basic screening line. They screened the bark and then started selling it, got more bark in and then it basically evolved into a full-scale bark operation.”
In 1997, they moved to their current 28-acre site on a former World War II airfield at Weston Longville in Norfolk, approximately 10 miles northwest of Norwich, where it continued to grow. “In 2003 we then expanded from bark and got into the garden waste. I think we were the first open window green waste recyclers in Norfolk,” recalls Andrews.
To develop the composting side of the business in 1998, Shane’s father Graham visited the RWM waste recycling exhibition, where he got to take a close look at some composting equipment. Although it was still early days for the sector, this led to the initial purchase of a Komptech Hurrikan windsifter and a Mustang drum screen, to help with the processing of garden waste.
This marked the beginning of a 25-year partnership between the two companies, which has played a critical role in the TMA Barks’s growth and success.
Making specialist grades
Today, the company processes about half a million cubic metres of bark, producing 28 different grades of product that vary according to the species of tree and size of the resulting bark, mulch and woodchip that it specialises in making.
“Customers will push us,” explains Andrews. “They say they want a particular size [of product] because they need a propagating bark for orchids. So we’re trying to make this specific product for growing. That’s when the Komptech stuff comes in, because the fixed line could only make a specific grade”
In 2014, TMA Bark acquired three Cribus 5000 drum screens – affectionately nicknamed ‘the trio’ – configured primarily to 5mm, 6mm and 8mm perforations. Having these lined up together enabled them to configure a time-saving process of running wood-based wastes through, in a way
that enabled one Cribus to feed another, which in turn feeds another.
“We’ll reprocess some of our high-volume base products [from the fixed line, which includes static Cribus’s] to then make finer grade specialist grades for these customers, most of it going to professional growing. We’re finding a lot more of that is coming now with the ban on peat. People want a bark alternative and they want certain sizes, special grades, special mixes and blends.”
The original trio have since been upgraded to the newer version of the Cribus 5000, Komptech’s high-throughput 250m3 drum screen which runs with an hybrid electric drive. Andrews notes how this has noticeably improved their operating costs: “They’re very fuel efficient. The diesel engine runs an electric generator and then the electric generator runs the machine. So fuel efficiency wise it’s fantastic.” Alternatively they can be plugged into mains power and run purely on electric.
He also cites their mobility as a valuable feature for their operation, easily moved on its trailer; it has notably enabled them to take it off site to do extra processing for some of their customers.
Green waste processing
Alongside processing wood-based products, TMA Bark operation now treats 25,000 tonnes of garden waste each year from Breckland Council, Broadland District Council and Norwich City Council, receiving RCV deliveries from these waste collection authorities direct to its site.
Once consignments have been vetted for quality, the green waste is put through a slow speed mobile Crambo shredder to create the windrows, which then goes through a 10 week composting schedule. It’s a machine that Andrews is full of praise for: “The Crambo is phenomenal. [They clearly spent a lot of money on that over the years in research and development… It’s down to tonnage, how much it can shred against its fuel return. In terms of how many tonnes it does, it’s really efficient. I don’t think there is another machine on the market that would beat the Crambo.”
Once the windrows are formed, they routinely go through a process of inversion using a Top Turn X63, spreading out the inverted material to create a new windrow. This aerates the green waste, enabling faster decomposition and helping to prevent compacting and excess heat buildup. Here again, the Komptech equipment plays a vital role in tackling the job. “I think it should be compulsory that every site has a Top Turn, I don’t know how you’d do it without one. It massively improves the product quality.”
The X63 is again a recent addition to the operation at TMA Bark, replacing an X60. According to Andrews, the key aspects of the newer model are that it improves accessibility to the engine for routine servicing and maintenance, as well as also making it easier for the operator to use: “It’s got an auto feature. So you can set it to auto and it’ll go down the window. And that’s very clever. It’ll go down the line. If it senses dense material, it’ll back off slightly. Let it clear, then keep going. The operator just has to basically just sit in there and keep an eye on it.”
The final stage of the green waste process is screening the organic material. Here, the company uses the Cribus drum screen alongside a Hurrifex, a wind sifter and destoner that Komptech no longer produces, which has since been succeeded by the Hurrikan and Stonefex.
In the winter, TMA Bark tends to make greater use of the L3 Star Screen. With a range of decks available, Andrews points in particular to its ability to make fine grades, for the bark side of the business as well as with the larger compost. “Particularly in wet months, if we’re struggling to screen, because the drum screens don’t really like the wet.”
With very little contamination, the resulting compost all conforms to PAS100 specifications. This means it can be used in specialist blends and mixtures for growing media that is well suited to the company’s customer base of professional growers in the bark world.
The expertise and equipment the operation has developed managing green waste has also enabled it to be approved as a site for treating diseased bark. Applying the X63, the material is similarly put into windrows to generate a high enough temperature to kill the pathogens, with regularly turning to ensure it all gets treated.
“Basically [the process] sanitises the bark and then it can be used again. But then also what we’ll do is we’ll form windrows with a blend. Row it all up into a windrow and then turn it over with a window turner to blitz it and mixes it all up properly. So [the Top Turn] has got a multi use.”
Long-term partnership
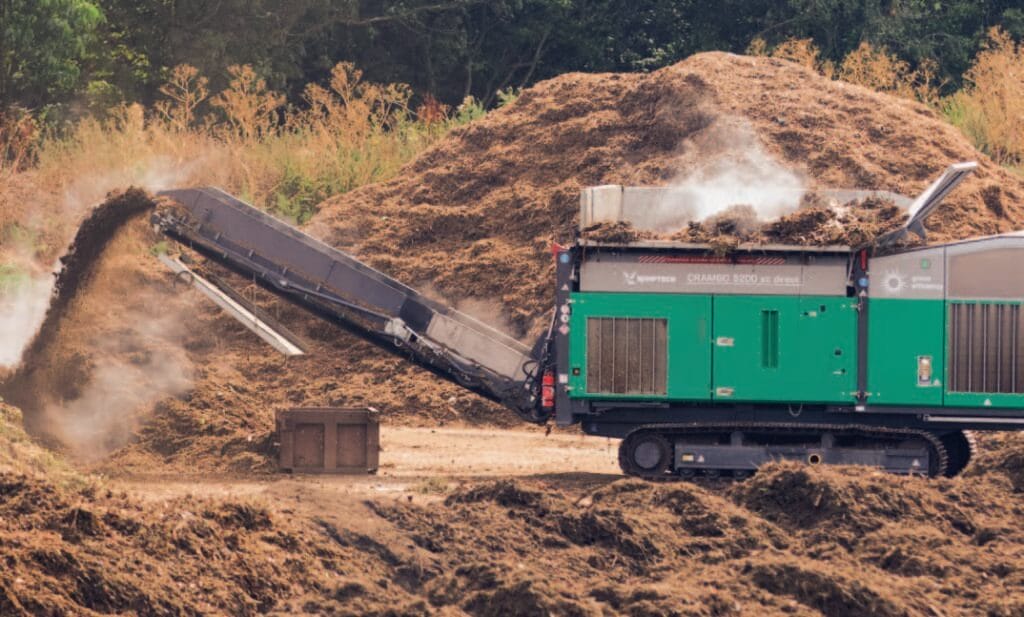
After almost 25 years of deploying Komptech machinery, TMA Bark has developed a close working relationship with the manufacturer and its UK dealer John Hanlon, which took on the franchise in 2016.
Andrews highlights the dependability and low maintenance costs as a key feature of his company’s long-standing loyalty to the manufacturer, adding: “Their machines, most of the time, are reliable. They look good as well. There’s no doubt about it. Komptech makes a good looking machine. And I’m a bit of a geek when it comes to machines.”
In the event of a breakdown, he highlights that John Hanlon is always quick to respond. “I ring them up, say, ‘It’s broke, can they fix it?’, and they send an engineer out, who comes out straight away. They’re typically with you the next day.”
According to Andrews, communication and the personal relationship has been key to a successful partnership: “I know a lot of the guys at Komptech, both in Germany and Austria. I can pick up the phone and talk to them anytime. Send them an email, they’ll get back to me and I know that I probably won’t get that anywhere else. And that goes a long way.”